The financial impact of a lift replacement doesn’t have to create overwhelming cash flow burden on your resort. Skytrac will create a custom, time-phased solution for your resort to upgrade your lift that matches your cash flow time frame.
Skytrac has created a program that steers away from complete installation to a phased lift replacement approach. We begin by prioritizing your lift’s highest risk issues and finish up with the minor necessary upgrades. Though experienced lifts differ in required work, we use an example of three phases. The phases are controlled by the resort’s decisions and cash-flow availability. When the phase periods are complete, your resort will have a significantly upgraded and reliable lift.
Phase 1
Year 1
Replace the Drive Terminal
See resort reference: Monarch Resort, Garfield Lift
Phase 2
Year 2 or 3
Replace Towers and Line Equipment
Possibly replace chairs depending on design (Riblet chairs incompatible with our sheaves)
See resort reference: Whitefish Mt. Relocate
Phase 3
Year 3 to 5
Replace Return Terminal
Chairs will be replaced if not completed in Phase 2
See resort reference: Pine Knob Chair 5
Financial Incentives
1. The resort will have control of the time that the work phases begin if dictated by cash flow.
2. With the contractual commitment, Skytrac can lock your resort in with pricing at time of signing. If the phases take longer by control of the resort, Skytrac will allow for cost increases only to match
the production price index, usually within 2-3% maximum.
3. Parts and components are sourced and fabricated in Salt Lake City, Utah.
Resort References
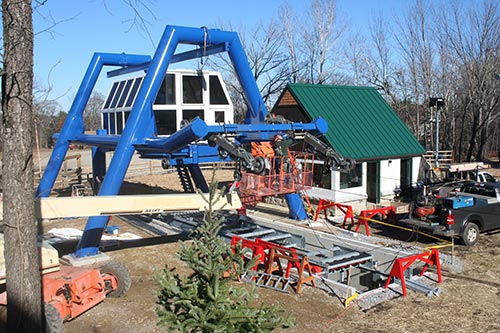
Pats Peak, NH
Relocation of a CTEC triple chair, installed hydraulic tension system, vault for loading conveyor.
Result of entire upgrade project: As Pats Peak has replaced a 54 year old double-chair with the significantly upgraded CTEC triple, the lift capacity has doubled from 800 to 1,600 passengers per hour.
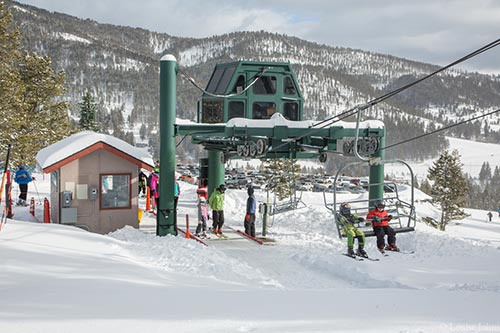
Bridger Bowl, MT
Relocation of 1999 CTEC. Installed new service brake and drop dog. Remaining equipment was reused.

Whitefish, MT
Relocation of a 1981 CTEC. Installed new lifting frames, catwalks, hydraulic tension system, service brake, coupling, extended some of the towers, modified grips.
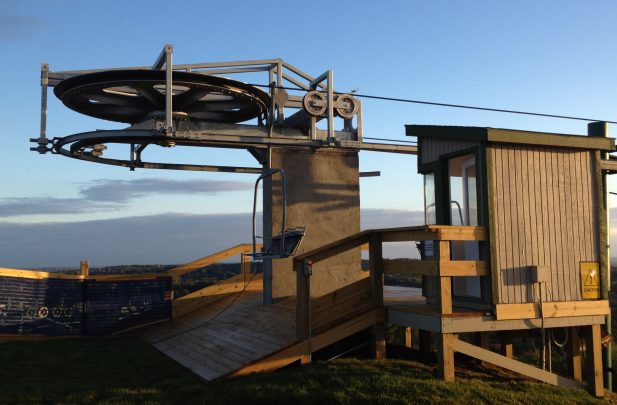
Pine Knob, MI
Replaced one fixed return terminal on chair #6 with guidage. Also replaced two drive/tension terminals on Riblet chairs #6 & 5. Remaining equipment was reused.

Keystone, CO
Replaced the bottom tension terminal on a Yan/Riblet lift with a new terminal and a complete new hydraulic tension control system.

Monarch, CO
Replaced two drive/tension terminals on two experienced Hall lifts, Garfield and Breezeway. Remaining equipment was reused.
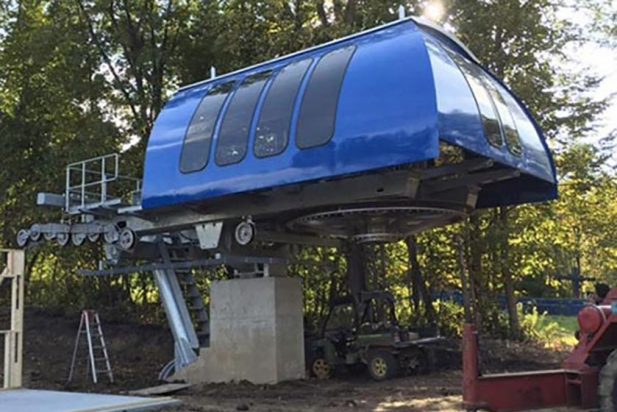
Alpine Valley, WI
Replaced a drive/tension terminal on a Hall. Remaining equipment was reused.